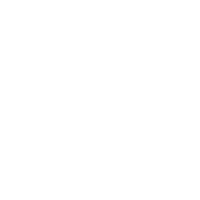
End of Life Tyres Plant (ELTs)End of Life Tyres Plant (ELTs)
TerniEnergia’s End-of-Life Tyre Recovery Systems implement a tyre grinding process that represents a technological alternative to traditional mechanical crushing processes.
In a first stage of treatment, ELTs are crushed into chips (shredded) between 50 mm and 100 mm in size. The tyre chips are ground in a flat-feed machine using the rotating roller principle. The grinding is carried out between the cylindrical rollers and a perforated circular plate. The process does not require the bead-barring phase in the case of truck tyre recycling. The press with an engine power of 2×250 kW can handle up to 4t/h of truck and car tyres at the inlet. After grinding, the steel wires and composite rubber are separated by magnets. In a first separation, the fine parts are extracted and the granulate is cleaned. The crude fraction and steel-composite rubber return to granulation. After granulation, the ground product is graded and cleaned in a multi-step process. The metal parts are separated by drum magnets and classified by sieves. The final classification for the separation of textile fibres is carried out in the zigzag separator and by means of separating boards. The clean granulate is packed in big-bags.
The capacity of the plant of 3t/h per granulation press can reach a capacity of more than 15,000 t/year.
Harmonic steel derived from ELTs is reused by steelworks for second smelting
The main uses of ELT’s rubber powder and granules are the following:
- Modified Asphalts
- Sports surfaces
- Insulation material
- Urban furniture, floors and artefacts
- Civil engineering works